Wytwarzanie sprężonego powietrza jeszcze jakiś czas temu było pomijalnym procesem z punktu widzenia ekonomii zakładu. W dobie rosnących cen energii, sprężarki generują znaczące koszty dla zakładu, a sprężone powietrze stało się kosztownym medium. Czy istnieją zatem metody, które są w stanie kontrolować szczelność instalacji sprężonego powietrza, zoptymalizować proces jego zużycia oraz zminimalizować występowanie jego wycieków i strat? Z odsieczą przechodzą ultradźwiękowe metody wykrywania nieszczelności w instalacjach sprężonych gazów. W jaki sposób szukać nieszczelności i tym samym oszczędności?
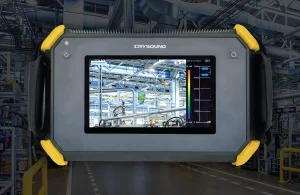
Czym jest sprężone powietrze?
Sprężone powietrze to powietrze o ciśnieniu wyższym niż początkowe (atmosferyczne), wytwarzane przy użyciu specjalistycznych urządzeń nazywanych sprężarkami powietrza. Wykorzystywane jest głównie jako medium do zasilania urządzeń pneumatycznych takich jak: pistolety lakiernicze, szlifierki, przecinarki, klucze udarowe, siłowniki itp.
W odróżnieniu od energii elektrycznej, gazu czy wody, sprężone powietrze jest wytwarzane głównie na miejscu, w danym zakładzie. Niestety mimo tego, nie zawsze nadzór nad nim prowadzony jest prawidłowo. W konsekwencji bardzo często dochodzi do generowania kosztów, na które, okazuje się, możemy mieć realny wpływ. Z naszego doświadczenia wiemy, jak ważna jest świadomość i ile potencjalnych strat niesie za sobą złe nadzorowanie linii ze sprężonym powietrzem. Dodatkowo brak odpowiedniej kontroli prowadzi do defektów, takich jak mikropęknięcia na zużytych wężach, złączach, rurociągach czy uszczelnieniach.
Wykrycie wycieków sprężonego powietrze jest trudnym procesem, a jego bezwonność i bezbarwność to niewątpliwie duże utrudnienie. Bardzo często są to dźwięki niesłyszalne pośród pracujących maszyn i urządzeń na halach produkcyjnych. Osoby pracujące w służbach utrzymania ruchu zwyczajnie je ignorują, ponieważ nie powodują zauważalnego zagrożenia życia, czy też niepowołanego zatrzymania linii produkcyjnej.
Jak odpowiednio kontrolować szczelność instalacji sprężonego powietrza?
Tradycyjne metody wykrywania wycieków sprężonego powietrza bywają czasochłonne i wymagają często zaangażowania sporej grupy ludzi. Dodatkowo mają ograniczoną skuteczność. Rekomendowaną przez nas metodą, jest wykrywanie nieszczelności za pomocą ultradźwięków.
Nieszczelności, poprzez przepływ turbulentny w miejscu wycieku, generują niesłyszalne dla nas ultradźwięki. Właśnie dlatego za pomocą ultradźwiękowych mierników oraz specjalistycznych kamer jesteśmy w stanie bez problemu zlokalizować miejsce i poziom wycieku. Dzięki temu możemy skutecznie i szybko kontrolować szczelność instalacji sprężonego powietrza.
Jak działają mierniki ultradźwiękowe?
Mierniki ultradźwięków to wielofunkcyjne urządzenia pozwalające na detekcję, pomiar oraz rejestrację ultradźwięków. Przyrządy te pozwalają kontrolować i analizować pracę łożysk, odwadniaczy, zaworów, przekładni oraz inspekcję elektryczną instalacji o napięciach powyżej 2 kV w kierunku wyładowań niezupełnych. Jednym z ich głównych zastosowań jest także wykrywanie przecieków w instalacji sprężonego powietrza.
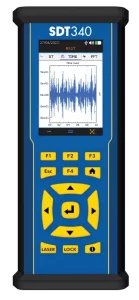
Mierniki przetwarzają sygnał ultradźwiękowy na dźwięk słyszalny dla człowieka, dlatego zestaw zawiera słuchawki. Przyrządy wyposażone są w kolorowy wyświetlacz oraz kilka przycisków funkcyjnych. Mierniki w swoim komplecie mają pełną gamę różnych sond pomiarowych. Do detekcji przecieków wykorzystujemy sondy bezkontaktowe: paraboliczną oraz elastyczną sondę bezkontaktową.
Wykonywanie kontroli szczelności instalacji sprężonego powietrza przy użyciu mierników polega na dokładnym skanowaniu instalacji za pomocą sond bezkontaktowych. Na wyświetlaczu urządzenia będziemy mogli dostrzec poziom ultradźwiękowy w dBmV oraz informacje dotyczące zmniejszenia lub zwiększenia wzmocnienia poziomu ultradźwięków, dostosowując się do poziomu hałasu środowiska pracy. Hałas wytwarzany przez pracujące maszyny będzie ignorowany.
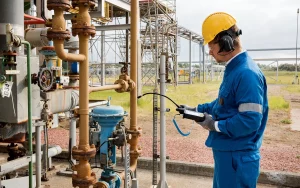
Więcej niż mierniki – kamery akustyczne
Obok mierników ultradźwięków mamy także do dyspozycji kamery akustyczne. Są to przenośne, przemysłowe rejestratory akustyczne obsługujące pasmo częstotliwości ultradźwięków.
Kamery wykorzystują specjalnie ukształtowaną matrycę mikrofonów wykonanych w technologii MEMS do gromadzenia danych o natężeniu emisji źródeł dźwięku. W kamerze o wysokiej rozdzielczości dźwięki te nanoszone są na obraz wideo w czasie rzeczywistym. Przemysłowe kamery akustyczne pomagają szybko wykryć wycieki gazu pod ciśnieniem i próżni w hałaśliwych instalacjach przemysłowych. Zasięg detekcji wycieków waha się w granicach od 0,3 m do aż 120 m.
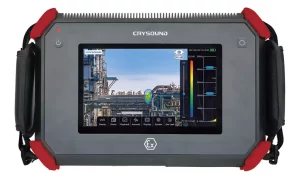
Przeprowadzanie kontroli wycieków sprężonego powietrza kamerami akustycznymi wykonujemy bardzo podobnie jak w przypadku mierników ultradźwięków. Musimy dostosować dwa parametry: zakres częstotliwości testowej oraz zakres dynamiki testu. Sygnał ultradźwiękowy jest przetwarzany na obraz widzialny w formie kolorowych „plam” w miejscu występowania nieszczelności. W momencie znalezienia wycieku możemy bezproblemowo wykonać i zapisać zdjęcie lub nagrać film. Kamery akustyczne dają nam możliwość szybkiej lokalizacji nieszczelności oraz przeskanowania bardzo dużej powierzchni w krótkim czasie.
Aby ułatwić pracę osobom nadzorującym szczelność instalacji sprężonego powietrza, stworzono aplikację mobilną na smartfony i platformy internetowe, do rejestrowania oraz generowania raportów pokazujących poziom wycieków po wykonaniu audytu w danej fabryce. Po zebraniu danych z przeglądu linii zarówno na platformie internetowej, jak i w aplikacji mobilnej, można dokonać przeglądu wykonanej pracy, rzeczywistych i potencjalnych oszczędności w złotówkach i ilość strat powietrza w m³/h.
Podsumowując, prawidłowo przeprowadzona, systematyczna diagnostyka instalacji sprężonego powietrza może znacząco obniżyć koszty związane z eksploatacją sprężonego powietrza i ograniczyć powstawanie generujących straty nieszczelności. W przeglądach instalacji pomogą nam urządzenia ultradźwiękowe – zarówno mierniki ultradźwięków, jak i akustyczne kamery. Metody te ułatwią nam dobrą praktykę dbania o instalację i zdecydowanie obniżą koszty eksploatacji tego medium.
Więcej informacji na temat kontrolowania wycieków sprężonego powietrza w naszym najnowszym numerze „Pod kontrolą”: